MANUFACTURING PROCESS
Microfiber Yarn Extrusion
This is a vertical process which usually takes place in a building that is 5 to 7 stories high. During this step, the raw materials (polyester and polyamide) are mixed together, in the proper proportions to achieve the desired final yarn composition. The mix is then heated to their melting point.
Bags of polyester pellets (PET)
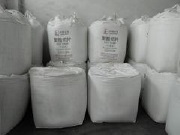
Close up on polyester pellets
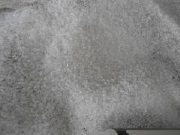
Foam insulation to conserve heat
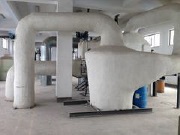
Testing of Microfiber Yarn
Before any additional step of transformation is performed on the yarn, it is of the utmost importance to test its structural characteristics. These tests are performed for two primary reasons. First at this stage of the process the physical characteristics of the yarn is highly representative of what the finished yarn will be, the subsequent processes introducing little variability. This is an opportunity to ensure that the yarn will comply with the desired specifications once it is finished. Second, frequent in-process testing allows for detection of slight deviations in key characteristics. These variations are not a problem and are actually normal, but once recognized allow for adjustment in manufacturing to make sure the finished yarn will always conform to the key parameters in the specification
Black doped dyed yarn
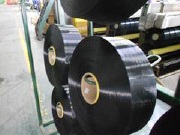
Filament cut preparation
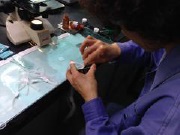
Observation of filaments
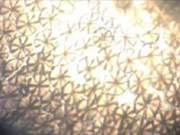
Conversion of POY into DTY and Spooling
The POY is subjected to heat and elongation in order to turn a conjugated polyester/polyamide yarn into Drawn Textured Yarn (DTY). The DTY yarn is what composes the majority of the finished product by weaving it around the FDY. Depending how much FDY is used for the substrate, the DTY needs to have a higher concentration in polyamide than the finished product, In order to obtain an 80% polyester / 20% polyamide finished towel for example, it is common to target a 77% polyester / 23% polyamide composition for the DTY.
Most spools are loaded with just white yarn, which gives the highest flexibility for subsequent steps in the process. A finished woven roll of fabric made with white yarn can always be dyed later to meet the demand of a specific finished product.
POY into DTY
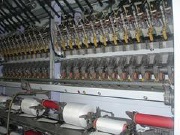
DTY to Spooling

Being Spooling
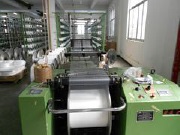
Weaving
Our weaving machines are using four lines of yarn. One for FDY and three for DTY. By adjusting the speed of each axle, the composition of the final product can be modified. In order to modify the weave a different program needs to be loaded into the weaving machine controller, sometimes different needles positioning or yarn re-routing is required to achieve the desired results. The output of weaving are large rolls of fabric from 1470 mm to 1780 mm. Depending on the type of weaving machine used, the daily output can vary between 400 and 1,200 Kg per day can be expected (900 to 2,600 Lbs.).
3 of the 4 axles of weaving machine
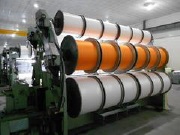
Initial weaving machine setup
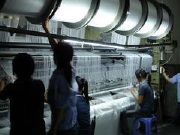
Adjustments before weaving
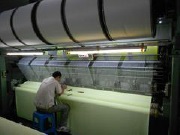
Quality check, Dyeing, Drying and Tensioning
Each roll is unrolled to pass in front of a light table in order to detect imperfections that could be created during the weaving process. The back-lighting allows to clearly see missing yarns (runners), holes, needles misalignment or any other defects. The areas with defects are marked on the fabric so that they can be removed from production.
Immediately after splitting and sometimes as part of a combined operation, the fabric is placed in large vessels, together with high quality pigments. The vessels are then pressurized and heated. Most vessels are steam heated, some are electric. The dyeing process ends with a rinsing cycle. All pigment residues and chemicals are collected and neutralized in large decantation tanks. The solid effluents are then transferred to a specialized plant for final treatment. No harmful chemicals are ever released in the environment. The clean water is reused to start the next dying cycle.
At the end of the dying process, the microfiber fabric is placed on a long horizontal machine which has a dual purpose. The fabric is running through the entire length of the machine, about 200 feet, to keep it at a constant tension while drying, which is very important to maintain the proper geometrical characteristics of the fabric, all the way to the finish product.
Digital Quality Monitoring of 4 yarns
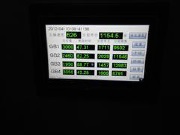
Splitting significantly increasing surface
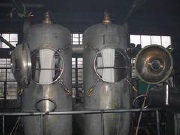
Constant tension maintained while drying
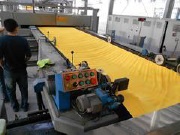
Cutting, Sewing, Final Inspection and Packaging
Rolls of fabric are unrolled in layers on top of one another, either by hand, or using an automatic machine. Depending on the type of fabric and the stability of the weave, there can be up to 150 layers. The top layer is then marked at specific intervals and a grid template drawn. The last step of this process is to cut at once through all of the layers with a vertical fabric blade. A variant for this process is fully automatic and also combines the sewing of the finished product. Another variant includes ultrasonic cut, where the edges of a towel are either cut straight or with a finish pattern, avoiding the need for sewing all together.
Individual pieces are surged, by adding a piping material and sewn on their entire perimeter. During this step a sew in label is inserted in the surging. The purpose of the label is to display the brand name, composition, sometimes care instructions.
A visual inspection makes the final determination if the product is suitable for packaging or not. If yes, bundles corresponding to the sell unit pack quantity are prepared, if not the individual piece is removed from the line and its sew in label cut off, a clear indication that the product is not suitable for retail as new. Depending on the type of defect, some of these products end up in bags of rags, when the efficacy of the product is not compromised and only a visual defect was observed.
Depending on the product, the sell unit could be packed in a clear polybag, a polybag with graphics, a clam shell, a cardboard box, a sleeve, the combinations are endless. A group of sell units is then placed into master cases to protect the product as well as to facilitate the transportation process.